AI in Manufacturing: Real-World Use Cases Driving Digital Transformation
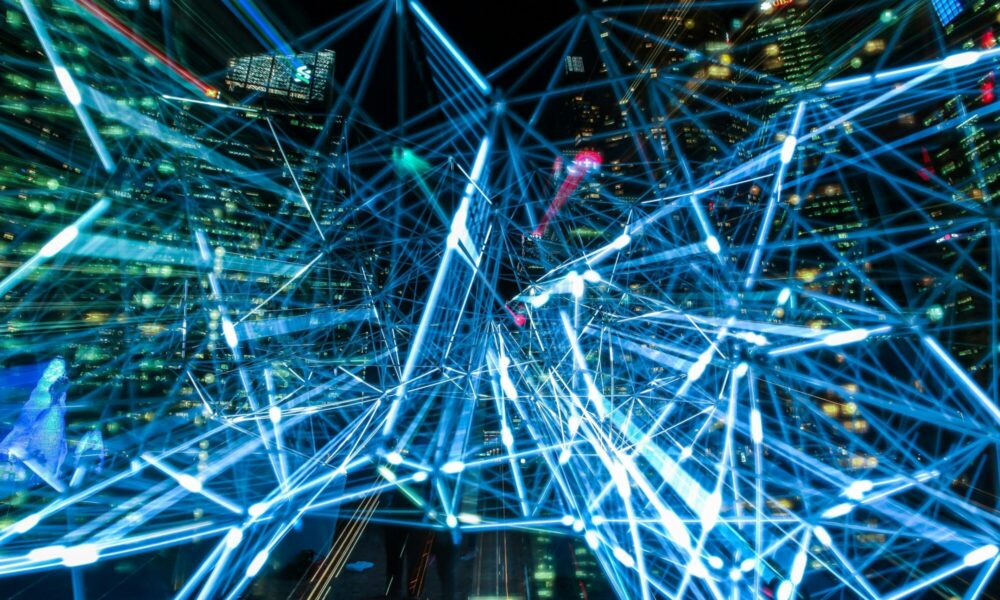
Manufacturing is experiencing a fundamental shift as artificial intelligence transforms production processes from rigid, rule-based systems into adaptive, intelligent operations. Adoption rates and market growth paint a compelling picture: 80% of manufacturers are either using or planning to adopt generative AI, while the AI in the manufacturing market is projected to reach $8.57 billion by 2025, up from $5.94 billion in 2024, an annual growth rate of 44.2%.
The evolution from traditional automation to AI-powered systems marks a pivotal moment in industrial history. Where legacy systems followed predetermined rules and required manual intervention for optimization, modern AI applications learn from data patterns, predict equipment failures, and autonomously adjust production parameters in real-time.
AI adoption extends beyond operational efficiency to fundamentally change how manufacturers approach product development, supply chain management, and customer service. The transition represents more than technology adoption—it signals a new era where data-driven insights enable predictive decision-making across entire product lifecycles.
The Strategic Importance of AI in Manufacturing
Manufacturers continue to face mounting pressure to deliver higher-quality and more sustainable products faster while maintaining cost efficiency and supply chain resilience. Conventional automation solutions, while effective for repetitive tasks, lack the adaptability to respond to volatile demand patterns, supply disruptions, and quality variations that characterize modern manufacturing environments. AI provides the intelligence layer that enables manufacturers to navigate these complexities through predictive capabilities and autonomous decision-making.
- The foundation for AI-driven manufacturing rests on a convergence of enabling technologies that have reached a state of industrial maturity.
- IoT sensors generate continuous streams of operational data from equipment, production lines, and environmental conditions.
- Today’s machine learning algorithms process this information to identify patterns and predict outcomes. Real-time analytics platforms transform raw data into actionable insights within milliseconds, enabling immediate responses to production anomalies or quality deviations.
- Cloud infrastructure provides the scalable computing power necessary to process vast datasets and support AI workloads without requiring massive investments in on-premises hardware.
This technological convergence enables AI to operate across the entire manufacturing value chain, from initial product design through final delivery. On the shop floor, AI-powered systems optimize production workflows, predict equipment failures before they occur, and maintain consistent quality through computer vision inspection systems.
Beyond production, AI algorithms enhance supply chain visibility by forecasting demand fluctuations, optimizing inventory levels, and identifying potential disruptions before they impact operations. The technology also extends into product development, where generative design algorithms help engineers explore multiple design configurations and optimize products for manufacturability, performance, and cost.
The strategic value lies in AI’s ability to transform manufacturing from a reactive to a predictive operation. Rather than responding to problems after they occur, AI-enabled systems anticipate issues, suggest optimizations, and automatically adjust processes to maintain peak performance. Shifting from corrective to preventive operations fundamentally changes how manufacturers approach efficiency, quality, and customer service.
AI Use Cases in Manufacturing: Where Intelligence Delivers Impact
The transition from theoretical AI potential to practical manufacturing applications is accelerating across industry sectors. These seven use cases represent areas where AI delivers measurable business value, transforming traditional processes through intelligent automation and data-driven insights.
Predictive Maintenance
AI-powered predictive maintenance transforms equipment management by monitoring machine health through sensor data to predict failures before they occur. Machine learning algorithms analyze vibration patterns, temperature fluctuations, and operational parameters to identify anomalies that indicate potential equipment issues.
According to McKinsey research, predictive maintenance can reduce machine downtime by 20% to 40%. This annual impact is significant across industries. 82% of companies have experienced unplanned downtime, averaging four hours per incident, costing industrial manufacturers an estimated $50 billion annually, according to Deloitte.
Automated Quality Inspection
Computer vision systems powered by AI detect defects in real-time with consistency that surpasses human inspection capabilities. Traditional manual inspection suffers from variability in defect detection rates, ranging from 60% to 90%, due to factors like inspector fatigue, whereas automated optical inspection maintains consistent accuracy across production runs.
These systems excel in electronics, automotive, and medical device manufacturing, where precision requirements demand reliable quality control. AI-driven inspection provides real-time intelligence, facilitating immediate identification and rectification of quality control issues. The result is significantly improved overall product quality, along with reduced labor costs and inspection bottlenecks.
Demand Forecasting and Inventory Planning
AI systems analyze complex data patterns from historical sales, market trends, and external factors to generate precise demand predictions that adapt continuously as new information becomes available. Machine learning models improve forecast accuracy over time by learning from prediction outcomes and adjusting algorithms accordingly.
Such capabilities enable manufacturers to optimize inventory levels, reduce waste from overproduction, and better allocate resources throughout their operations. AI forecasting excels at predicting customized product demand by analyzing order history and customer preferences, particularly benefiting manufacturers offering personalized or made-to-order products.
AI in Production Scheduling
AI-optimized dynamic production scheduling prioritizes tasks and resources based on real-time availability, deadlines, and changing production requirements. These systems analyze vast amounts of data, including production capacity, machine performance, inventory levels, and customer demand, to continuously optimize workflows.
Seventy-six percent of manufacturers report that AI technologies have significantly improved their production scheduling accuracy while reducing production downtime. AI-powered scheduling adapts quickly to unexpected events, such as machine breakdowns or supply chain disruptions, automatically re-optimizing schedules to minimize operational impact and maintain efficiency.
Autonomous Robotics and Material Handling
AI-enabled robots and autonomous material handling systems improve efficiency in picking, packing, and repetitive motion tasks by adapting to dynamic production environments. Autonomous Mobile Robots (AMRs) and Automated Guided Vehicles (AGVs) leverage real-time data to optimize routing and streamline workflows without human intervention.
These systems offer high flexibility compared to traditional fixed automation, adapting to changes in layout, product types, and operational needs in real-time. Collaborative robots (cobots) learn from operator behavior patterns, enhancing safety through AI sensors and collision avoidance while reducing human-related accidents in manufacturing environments.
Generative Design in Engineering
AI-powered generative design enables simultaneous exploration of hundreds of thousands of design concepts, accelerating product development through automated creation of optimized solutions. This approach allows engineers to input performance goals, material constraints, and manufacturing requirements, and then generate multiple design iterations that meet specified criteria.
Generative design significantly reduces prototyping time while enabling mass customization and faster design timelines compared to traditional sequential design processes. Many leading industry software providers are incorporating AI features into their modeling and simulation applications, making generative design more accessible through natural language processing interfaces.
Energy Optimization and Sustainability
AI systems identify excessive energy usage patterns and recommend corrective actions that improve operational efficiency while supporting environmental sustainability goals. Predictive maintenance algorithms contribute to energy optimization by detecting equipment inefficiencies, such as motors consuming more power than usual due to wear and tear.
According to the U.S. Department of Energy, predictive maintenance can yield energy cost savings of 8% to 12% compared to preventive maintenance and up to 40% compared to reactive maintenance approaches. These systems analyze energy consumption data across manufacturing operations to identify opportunities for optimization, reduce waste, and lower operational costs, while helping manufacturers meet their ESG commitments and regulatory requirements.
AI in Manufacturing Examples: Real-World Case Studies
Industry leaders are moving AI from the lab to the factory floor with impressive results. These implementations show how manufacturers transform traditional processes into intelligent operations that deliver real business value.
Automotive: AI-Driven Quality Inspection Systems
General Motors has revolutionized vehicle quality control through its partnership with UVeye, implementing AI-powered inspection systems that conduct comprehensive vehicle scans during the manufacturing and post-production stages. These advanced systems utilize AI algorithms to analyze vehicle conditions with remarkable precision, reducing inspection times while elevating overall quality standards. The technology addresses a critical industry challenge where traditional manual inspections can miss defects due to human oversight or fatigue, while AI-powered systems maintain consistent, tireless scanning for even the minutest imperfections.
Aerospace: Digital Twins and Predictive Maintenance
The aerospace industry leverages AI-powered digital twins to simulate component wear and predict maintenance needs with unprecedented accuracy. Digital twin technology creates virtual replicas of physical aircraft components that grow richer as parts experience real-world conditions, incorporating data from embedded sensors and IoT feeds to simulate performance under various flight scenarios. When an engine blade is tracked through its entire lifecycle—from alloy selection to current heat exposure—technicians can virtually stress-test components and pinpoint early-stage failure before physical signs appear.
Airbus has implemented predictive maintenance systems that analyze vast amounts of operational data to forecast equipment failures and optimize maintenance scheduling. These AI systems process information from thousands of sensors across aircraft systems, identifying patterns that indicate potential issues weeks or months before they would manifest as actual problems.
Electronics: AI-Enhanced Production Optimization
Samsung Electronics has extensively integrated AI into its consumer electronics manufacturing processes to manage the high complexity of assembly lines for smartphones, televisions, and other devices. The company utilizes AI to automate complex assembly operations, improving speed and accuracy while reducing labor costs. At the same time, AI-driven quality control systems detect defects and ensure consistent product standards across millions of units. Samsung’s predictive analytics systems optimize supply chain operations by anticipating market demands and managing inventory efficiently, thereby reducing overproduction and enabling a rapid response to market trends.
AI and Data Governance
As manufacturers deploy AI tools, employing robust data governance becomes critical to balance innovation with security. AI systems must respect the same access controls and compliance policies as human users—especially when handling sensitive product data. Without proper guardrails, AI risks exposing intellectual property or violating regulations.
Companies like Aras address this challenge through a three-tiered data classification system that defines access rules based on data sensitivity:
- Unrestricted Data: Publicly available information that doesn’t reveal proprietary details (e.g., product specifications for customer documentation).
- Sensitive Data: Requires role-based access controls (e.g., design schematics shared selectively with suppliers or partners).
- Confidential Data: Never exposed to AI (e.g., trade secrets, patented formulas, or classified materials).
Strict classification enables dynamic governance where AI access adapts automatically based on user roles, specific use cases, and security policies. By integrating these guardrails directly into digital thread platforms, manufacturers can leverage AI while maintaining strict control over sensitive data and ensuring compliance with industry regulations.
AI Use Cases in Manufacturing That Enable the Digital Thread
The digital thread represents the seamless flow of information across the entire product lifecycle, from initial design concepts through production execution and ongoing service operations. AI transforms this theoretical concept into a practical reality by creating intelligent connections between previously siloed systems and data sources. Modern AI applications aggregate and interpret disparate data sources that may be inconsistent or unreconciled, enabling manufacturers to maintain comprehensive visibility into product evolution while supporting real-time decision-making across engineering, manufacturing, and service functions.
The AI-enabled digital thread enhances traceability by automating data collection and analysis throughout the manufacturing process, enabling the extraction of valuable insights from large volumes of real-time data that traditional methods struggle to achieve. Companies like Schaeffler and Bridgestone demonstrate this capability in action, using AI agents to allow frontline workers to access detailed information immediately during unexpected downtime and interact efficiently with factory data to improve yield and quality. This approach transforms manufacturing from reactive operations to predictive, adaptive systems that maintain cross-functional alignment while enabling rapid response to changing market conditions and customer requirements.
Embracing the Future of AI in Manufacturing
AI in manufacturing delivers measurable ROI today through predictive maintenance, quality optimization, and production efficiency improvements. Organizations should explore AI use cases that align with their specific operational challenges to gain competitive advantages. As data ecosystems mature, AI will shift from optional to essential for manufacturers competing in digital markets.
Source: AI in Manufacturing: Real-World Use Cases Driving Digital Transformation